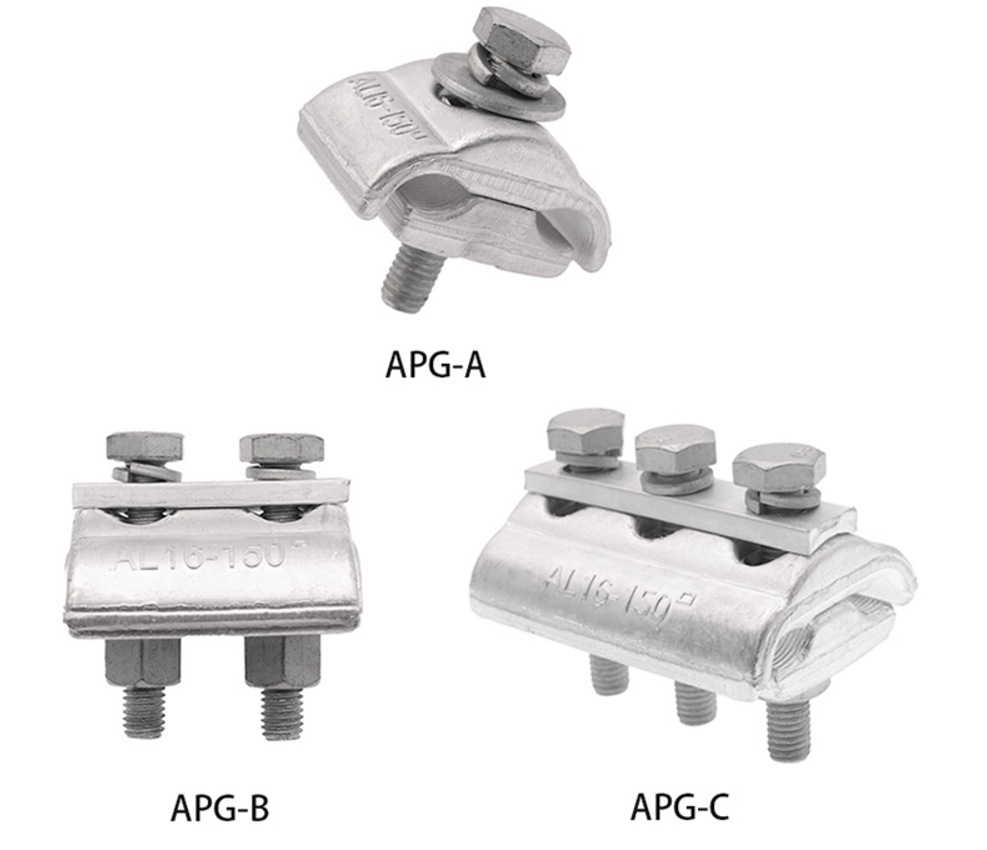
When it comes to the application of bolted wire connector clamps, the choice of bolt material plays a crucial role in determining performance, durability, and reliability. Three common types of bolts used in this context are Dacromet - coated iron bolts, hot - dip galvanized bolts, and stainless - steel bolts, each with its unique characteristics and application scenarios.
Dacromet - coated iron bolts are a popular choice for their exceptional corrosion resistance. The Dacromet coating, a thin, zinc - based, inorganic, non - electrolytic coating, provides a barrier against rust and chemical corrosion, making them suitable for use in harsh environments such as coastal areas, industrial zones with high levels of pollutants, or regions with high humidity. They also offer good heat resistance, withstanding temperatures up to 300°C without significant degradation. However, Dacromet - coated bolts are relatively expensive compared to other options, and their mechanical strength may be slightly lower than that of some heat - treated steel bolts.
Hot - dip galvanized bolts are another widely used option. The hot - dip galvanizing process involves immersing the bolts in a bath of molten zinc, which forms a thick, protective layer on the surface. This zinc layer provides excellent corrosion protection, especially for outdoor applications where the bolts are exposed to the elements. Hot - dip galvanized bolts are more cost - effective than Dacromet - coated bolts and have good mechanical properties, including high tensile strength and good ductility. However, the galvanized layer may be damaged during installation or handling, reducing its corrosion resistance. In addition, the appearance of hot - dip galvanized bolts may not be as aesthetically pleasing as other options.
Stainless - steel bolts are known for their high strength, excellent corrosion resistance, and long service life. They are made from an alloy of iron, chromium, nickel, and other elements, which gives them superior resistance to rust, oxidation, and chemical attack. Stainless - steel bolts are suitable for use in a wide range of applications, including marine environments, food processing plants, and chemical industries, where high levels of corrosion resistance are required. They also have a clean, attractive appearance, making them a popular choice for applications where aesthetics are important. However, stainless - steel bolts are the most expensive option among the three, and their high cost may limit their use in some applications.
In conclusion, the choice of bolt material for wire connector clamps depends on various factors, including the application environment, performance requirements, and cost considerations.
Dacromet - coated iron bolts are ideal for harsh environments where high - level corrosion resistance and heat resistance are needed; hot - dip galvanized bolts offer a cost - effective solution for general outdoor applications; and stainless - steel bolts are the best choice for applications requiring high strength, excellent corrosion resistance, and a long service life. By understanding the differences between these materials, engineers and installers can make informed decisions to ensure the optimal performance and reliability of their electrical connections.